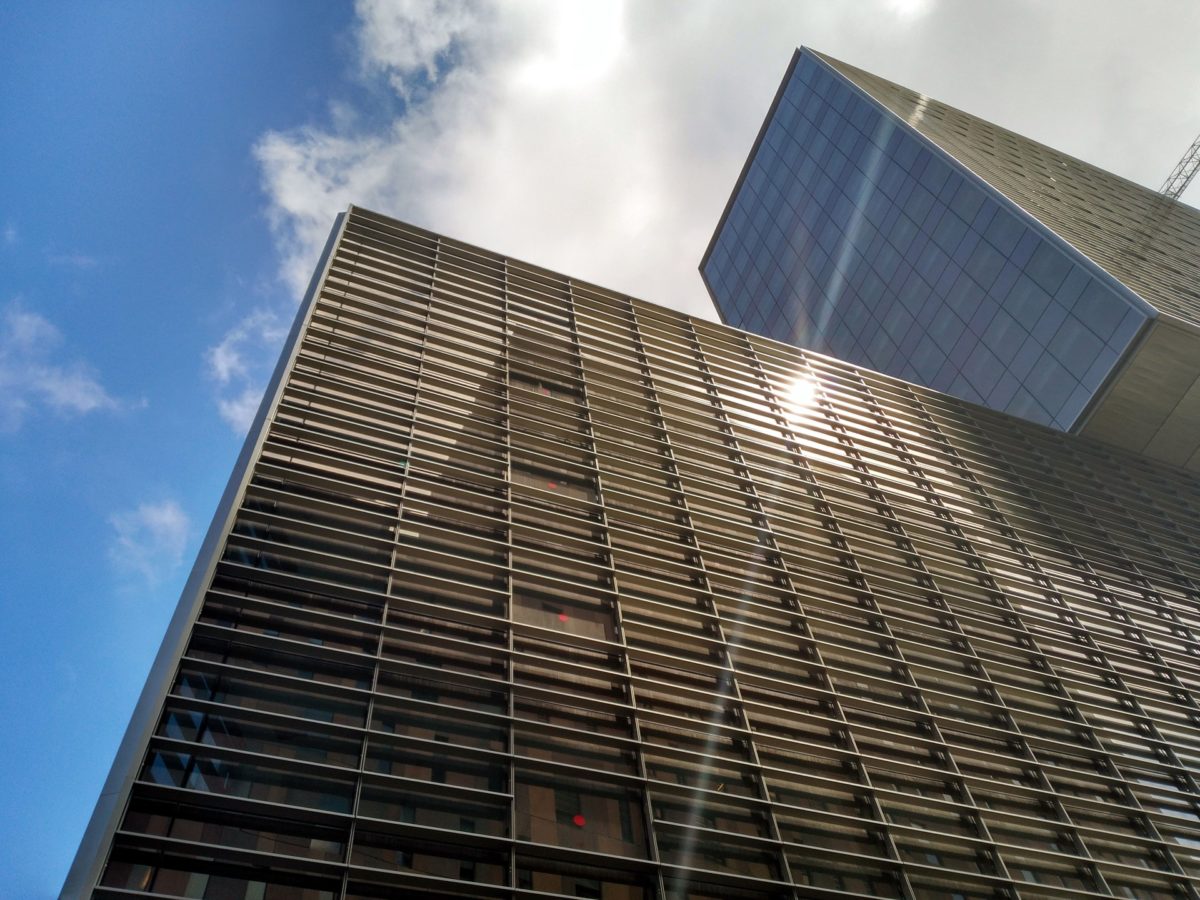
Researchers in Iran developed a passive solar module cooling method using silicon carbide porous ceramic. When combined with phase change materials, the technique reportedly boosts panel performance by up to 7.4%.
A group of researchers from Iran’s University of Tehran has developed a porous silicon-carbide (SiC) ceramic that, especially if used in combination with a phase change material (PCM), can reduce solar module temperature and increase its efficiency.
PCMs can absorb, store, and release large amounts of latent heat over defined temperature ranges. They have often been used at the research level for PV module cooling and the storage of heat.
The novel passive cooling technology was tested in two different configurations – SiC porous ceramic with water and SiC porous ceramic with phase change material (PCM) – and their cooling performance was compared to that of other passive techniques such as cellulose pads with water, aluminum shavings with PCM, and metal pellets with PCM.
“While numerous studies have investigated various cooling techniques, few have incorporated a comprehensive economic analysis to ascertain the feasibility and cost-effectiveness of these materials,” the scientists said. “This study bridges this gap by proposing the use of inexpensive, sustainable materials for passive cooling to not only improve the electrical and thermal performance of PV panels but also to provide a cost-benefit analysis that demonstrates the economic viability of the proposed solution.”
The metal pellets were recovered from wastes of ball bearings, the aluminum shavings from industrial waste, and the cellulose pads were taken from air cooling devices. The SiC porous ceramic medium was manufactured with black SiC, green SiC, alpha-aluminum oxide, ball clay, colloidal silica, and polyvinyl alcohol (PVA) 2088.
The selected PCM was residue wax, with an oil content of 30% to 50% and a melting point of 40 C to 45 C. “The main criteria for selecting the PCM type were to be low cost, have a melting point of less than 45 C, be less common in the literature, and be available in the local market,” the team explained their choice.
For their analysis, the research team applied all the cooling media onto a 20 W polycrystalline silicon module, with each of the five configurations being tested for three consecutive days in Tehran. Temperatures were monitored using a digital temperature data logger. Further economic analysis was based on local market conditions, with an assumed system lifetime of 20 years and an inflation rate of 10%.
“The most significant temperature reduction in the PV panel was observed in the scenario utilizing metal pellets and PCM, representing a 16.3% decrease compared to a PV panel without a cooling system,” the scientists said. “Additionally, an average improvement in electrical efficiency of 10.6% was attained. Economic analysis unveiled that the cooling scenario employing metal pellets integrated with PCM exhibited the lowest levelized cost of energy (LCOE) among the proposed cooling methods, amounting to $0.134/kWh.”
The SiC porous ceramic with PCM was able to achieve a temperature reduction of 10.9% and an electrical efficiency increase of 7.4%, with an LCOE of $0.165/kWh. The cooling medium made of Aluminum shavings with PCM recorded a temperature decrease of 9.3%, an efficiency increase of 5.3%, and an LCOE of $0.139/kWh.
“The water-based cooling scenarios, incorporating SiC porous ceramic and cellulose pads, yielded a temperature drop of less than 4.2% and an electrical efficiency improvement of less than 3.2% compared to the standalone PV panel. Additionally, the resulting LCOE ranged from $0.155 to $0.166/kWh,” the team concluded.
The results were presented in “Experimental investigation of photovoltaic passive cooling methods using low-cost metallic, ceramic, and cellulose porous media,” published in Energy Conversion and Management: X.
This content is protected by copyright and may not be reused. If you want to cooperate with us and would like to reuse some of our content, please contact: editors@pv-magazine.com.
Source link